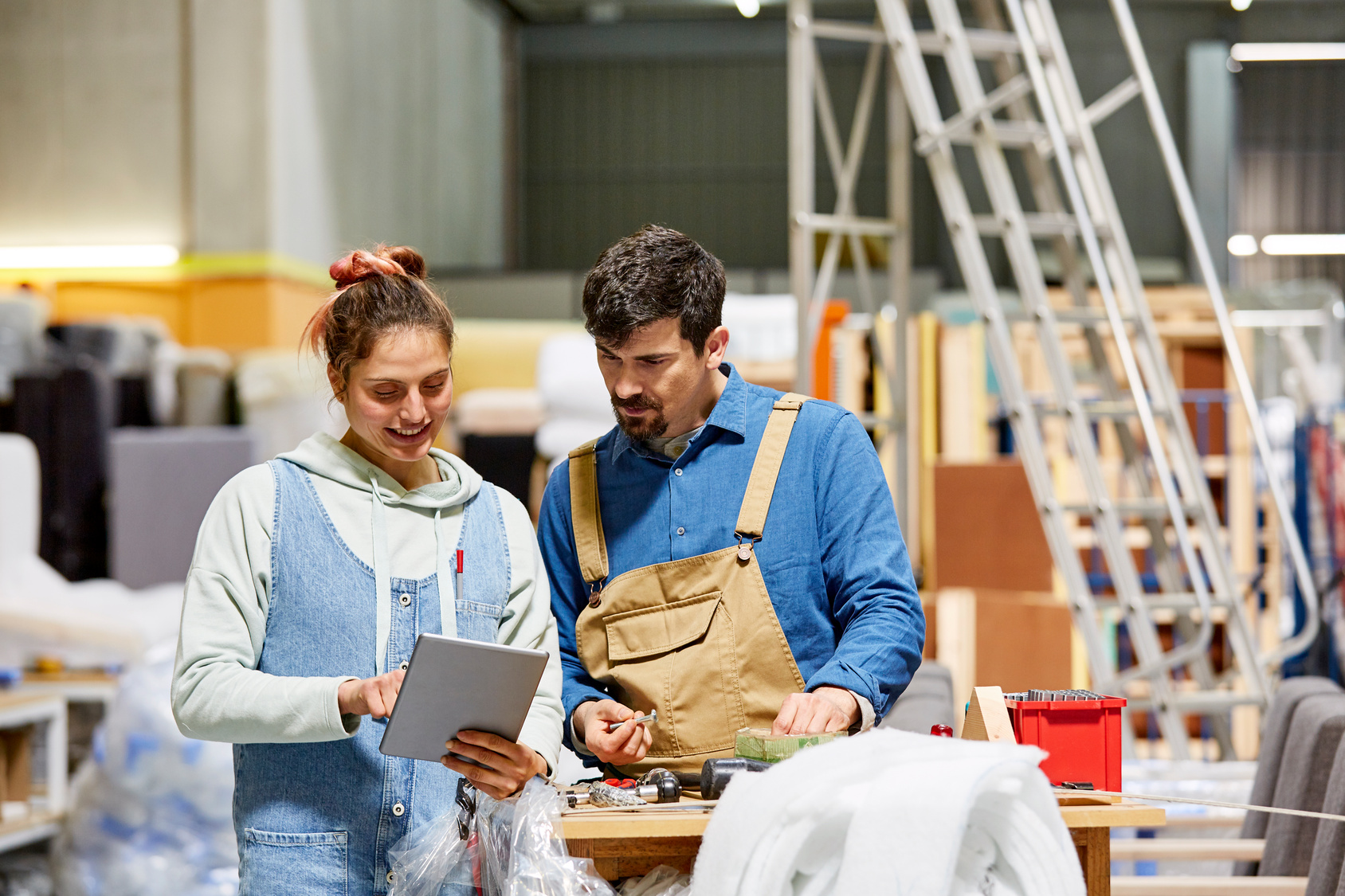
19 Nov How AiFi’s Spatial Intelligence Unlocks Hidden Cost Savings in Manufacturing
In today’s competitive manufacturing landscape, remaining profitable requires more than just managing visible costs. Several operations can bleed money through hidden and often overlooked inefficiencies. It can be even more challenging to manage these invisible expenses because they rarely show up in standard financial reports or daily operations logs. They silently drain resources over time, creating significant financial and operational setbacks.
What if there were a way to uncover these hidden costs? With spatial intelligence technology, there is. Spatial intelligence provides manufacturers with real-time insights into every corner of their operations. By identifying bottlenecks, preventing costly incidents, and empowering data-driven decision-making, AiFi’s spatial intelligence technology allows manufacturers to cut out inefficiencies and optimize their bottom line.
Revealing the Hidden Costs Draining Your Bottom Line
Most manufacturing managers are adept in tracking and overseeing direct costs - such as labor, materials, and utilities. However, expenses resulting from labor inefficiencies, underutilized assets, safety incidents, and security breaches, often go unnoticed. These expenditures may appear minor individually, but together, they create a substantial financial burden and directly affect manufacturing efficiency. Here are the four main areas where unseen costs frequently impact manufacturers:
Labor Inefficiencies
Labor inefficiencies are commonly unrecognized but may be among the most costly issues when analyzing manufacturing efficiency. Over time, unnecessary labor expenses pile up from overstaffing, uneven task allocation, and communication problems. For example, overstaffing happens when there is an overage of employees in a low-activity area, producing a drain on payroll without adding significant value to operations.
Poor task allocation is an additional area where costs inflate without notice, draining manufacturing efficiency. Workers may be assigned tasks that don’t fully utilize their skills or time, leading to a lack of productivity. Time wasted in tracking down equipment, waiting for tasks, or clarifying instructions further augments these inefficiencies. The cumulative effect is a loss of productivity, elevated labor costs, and, ultimately, a significant impact on the bottom line.
Underutilized Assets
Have you ever peeked inside a manufacturing facility? If so, you’ve seen first hand how they’re filled with hundreds of expensive assets. This is because manufacturing relies heavily on high-value assets, such as machinery, tools, and technology. However, when these assets sit idle, either due to scheduling conflicts, bottlenecks, or a lack of real-time utilization visibility, they add little to the operation’s overall manufacturing efficiency. Asset underutilization is a commonly overlooked form of waste that depletes capital without contributing value.
For instance, a bottleneck in one part of the production line might cause other equipment to sit idle, wasting valuable production time. Likewise, output and revenue potential can be impacted when machinery isn’t scheduled efficiently, causing downtime. When equipment is regularly underutilized, it doesn’t only hurt productivity—it also affects equipment ROI and drives up maintenance costs from sporadic use.
Safety Incidents
Safety is a priority in any manufacturing environment, but even in today’s modern world, workplace accidents and incidents continue to happen. Beyond the immediate human cost, these accidents can lead to financial setbacks in several ways. Incidents may result in medical expenses, increased insurance premiums, and potential legal issues - let alone timeline disruptions and productivity drops. These mishaps can also erode employee morale and cause higher turnover rates, both of which have even further cost implications to manufacturing efficiency.
The long-term effects of a hazardous work environment can be extreme. Employees might hesitate to work near high-risk areas or feel less engaged during work hours. As safety-related costs accumulate, they not only cause strain on financial resources but also reduce operational manufacturing efficiency and cause harm to the company's reputation.
Security Breaches
Security breaches, from unauthorized access, to theft and vandalism, can quickly dismantle manufacturing efficiency. When these security issues happen, the results manifest in direct and indirect costs, such as lost inventory, damage to equipment, and potential interruptions to production. Not to mention, unwanted access to restricted areas could lead to data theft, product tampering, and expensive damages.
The financial losses associated with security incidents go beyond immediate replacement costs - customer trust can wear down, partnerships damaged, and production hindered. Security issues will significantly impact both short- and long-term profitability if not addressed properly and in a timely manner.
AiFi’s Spatial Intelligence: Your Data-Driven Solution for Cost Optimization
AiFi’s spatial intelligence platform goes beyond basic metrics, providing a comprehensive view of operations in real time. Here’s how it can help manufacturing facilities identify, understand, and eliminate invisible costs:
Real-Time Visibility into Operations
AiFi’s spatial intelligence solution provides real-time tracking of materials, equipment, and personnel. This level of insight allows manufacturers to better manage and optimize workflows, ensuring resources are being utilized as efficiently as possible. AiFi’s platform can detect and monitor lags in task allocation and bottlenecks that delay production, enabling facilities to make necessary adjustments immediately.
By following movements and patterns, spatial intelligence also allows manufacturers to anticipate where overstaffing or task redundancies may occur. This ability can guide better task assignments, prevent wasted time, and create an efficient flow of operations to boost manufacturing efficiency. Using spatial intelligence to gain real-time visibility, managers have control over each aspect of the operation, leading to more streamlined processes and reduced labor costs.
Proactive Safety Management
Safety is a core focus in any manufacturing facility, and spatial intelligence can enhance safety through real-time monitoring and proactive alerts. Spatial intelligence detects potentially high-risk situations, such as blocked exits or equipment malfunctions, which could pose a safety risk. It also recognizes unsafe behavior patterns, allowing facility managers to address issues before they lead to accidents.
For instance, if a worker routinely enters hazardous areas without proper protective gear, the system can issue an alert, allowing managers to intervene. This proactive safety management minimizes the likelihood of incidents, which in turn helps avoid costly disruptions, insurance claims, and legal ramifications. The ability to monitor and implement a safer workplace leads to a more stable, motivated workforce and fewer hidden costs associated with accidents.
Enhanced Security Measures
Security is another area where spatial intelligence shines. Manufacturing facilities commonly require controlled access to protect valuable assets and sensitive information. Spatial intelligence offers features like tailgating alerts, which help prevent unauthorized individuals from entering restricted areas by following after a facility employee. Additionally, the platform provides anomaly detection alerts, flagging unusual activity in higher-risk areas.
By implementing these enhanced security measures through spatial intelligence, facilities can reduce the risk of theft, vandalism, and operational disruptions, boosting manufacturing efficiency. Security breaches are costly, not only in terms of immediate financial loss but also due to production downtime. AiFi’s security features help facility managers gain peace of mind and a way to proactively manage security risks, creating a safer and more efficient work environment.
Data-Driven Decision-Making
One of the most powerful features of AiFi’s spatial intelligence platform is its ability to support data-driven decision-making. The platform’s real-time data insights allow managers to make informed decisions about staffing, asset utilization, process improvements, and safety protocols. For example, by understanding which equipment is underutilized, facility managers can make adjustments to increase productivity and maximize ROI for ideal manufacturing efficiency. Data-driven decision-making also enables better long-term planning.
With access to historical data, manufacturers can spot trends, identify recurring bottlenecks, and develop strategies to prevent inefficiencies from arising in the future. This approach ensures that managers can focus resources on areas that deliver the most value, further reducing operational costs and increasing revenue for your organization.
Final Thoughts
Hidden costs are a consequential but often unrecognized burden on manufacturing facilities and operations. Spatial intelligence technology provides the visibility needed to expose and address these invisible costs, empowering manufacturers to optimize every aspect of their operations.
By offering real-time data, enhanced security measures, and actionable insights, AiFi’s spatial intelligence platform enables manufacturers to cut down on unnecessary costs and maximize efficiency. For companies aiming to stay competitive, reduce operational waste, and boost profitability, request a demo today or explore our blog for more insights on optimizing your manufacturing operations.