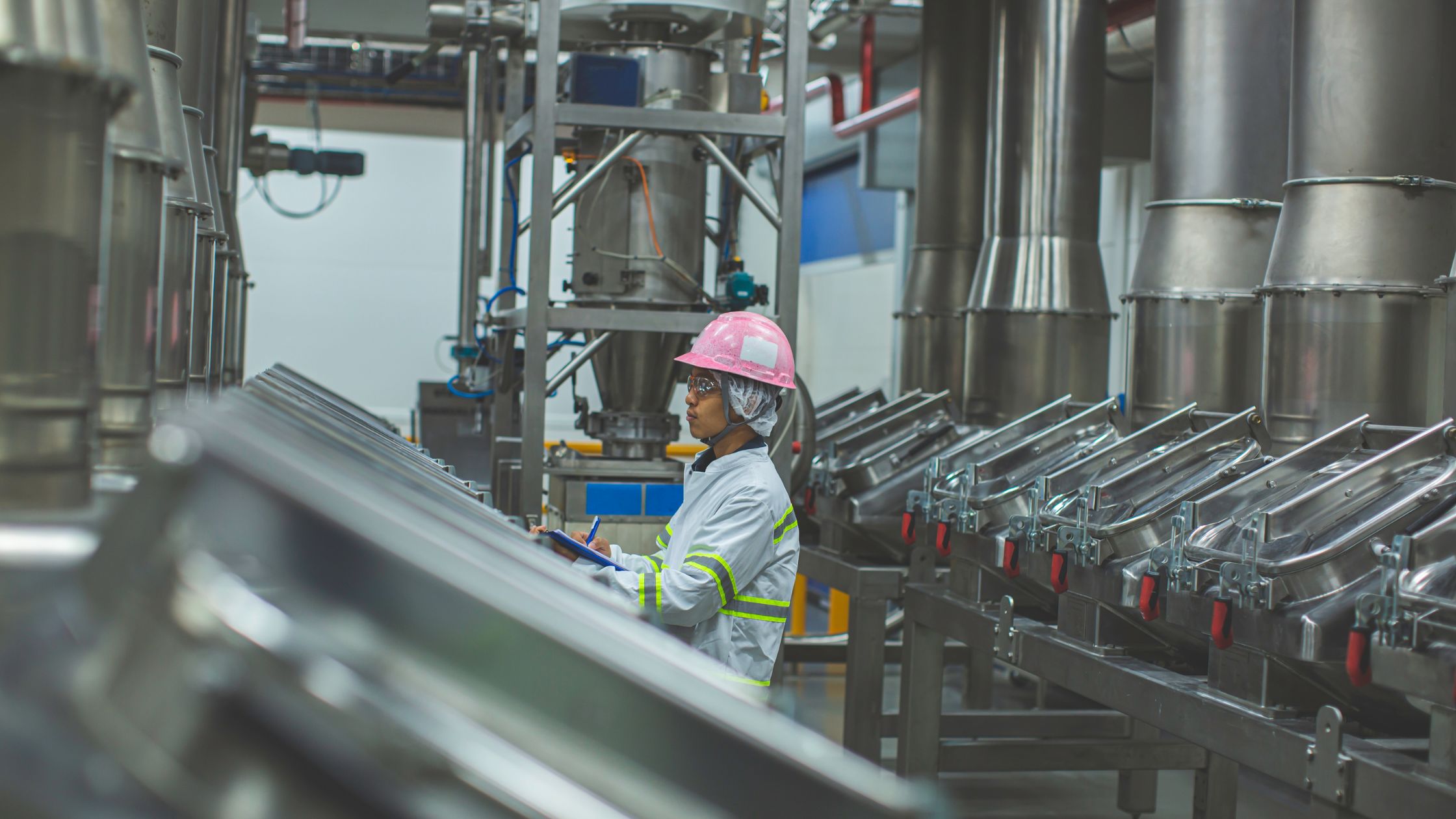
31 Oct 8 Signs Your Manufacturing Operation Needs a Spatial Intelligence Upgrade
In this post, we'll reveal 8 signs that your manufacturing or distribution operation is ripe for a spatial intelligence upgrade. If any of these resonate, you could be missing out on significant opportunities to boost manufacturing efficiency, enhance safety, and outpace the competition.
Let's explore these indicators and uncover the potential of a truly intelligent facility.
1. You're Constantly Battling Bottlenecks
Bottlenecks are like those traffic jams that seem to appear out of nowhere, grinding everything to a halt. In manufacturing and distribution, they're not just annoyances - they're serious threats to your bottom line. These choke points in your production line or warehouse don't just slow things down; they create a domino effect of inefficiency. One small holdup can lead to delayed orders, increased labor costs, and issues as workers rush to catch up.
But here's the thing: bottlenecks aren't always obvious. Sometimes they're hiding in plain sight, masquerading as "the way things have always been done." Imagine having a real-time, 3D map of your entire facility, showing the flow of materials, movement of workers, and status of each piece of equipment. That's what spatial intelligence provides. It uses a network of advanced sensors and cameras, all feeding data into AI-powered analytics systems. This setup doesn't just show you where bottlenecks are happening - it helps predict where they're likely to occur next.
2. You Have High Rates of Downtime
When machines suddenly break down, it's not just a temporary pause - it's a full-blown crisis that can derail your entire production schedule. An average large plant loses 25 hours a month to unplanned downtime. These disruptions don't just eat into your productivity; they can lead to missed deadlines, ballooning costs, and even quality issues as you scramble to catch up.
But what if you could see these breakdowns coming before they happen? By using a network of smart sensors and AI-powered analytics, spatial intelligence keeps a constant eye on your equipment's health. Suddenly, you're not frantically reacting to emergencies, you're calmly scheduling maintenance during planned downtimes.
3. You Struggle to Track Inventory and Assets
Ever feel like your warehouse is playing an endless game of hide-and-seek with your inventory? Not knowing exactly where your materials, equipment, or finished goods are at any given moment is more than just frustrating - it's a major liability. This lack of real-time visibility can lead to production delays, overstocking, stockouts, and even lost assets.
By leveraging technologies like RFID tags, IoT sensors, and advanced tracking software, spatial intelligence creates a real-time, 3D digital twin of your entire inventory ecosystem. You won’t be guessing where things might be, you’ll know exactly everything is, how much you have, and even how it’s moving through your facility. This level of insight doesn't just save time and reduce stress - it opens up new possibilities for the manufacturing efficiency of your entire operation.
4. Your Workers Spend Too Much Time Searching for Things
Your skilled workers, the backbone of your operation, spend hours each week just looking for stuff. It sounds absurd, but it's a reality in many manufacturing facilities. When employees can't quickly locate the tools, materials, or information they need, it's not just a minor inconvenience - it's a major drain on productivity. This constant searching doesn't just slow things down; it leads to frustration, errors, and a general sense of inefficiency that can permeate your entire operation.
Spatial intelligence turns your facility into a smart, connected space. With precise location tracking and intuitive interfaces, workers can instantly pinpoint the exact location of any item they need. No more wandering the aisles or digging through cluttered storage areas.
5. You Have Limited Insight into Worker Productivity
In many manufacturing operations, gauging productivity is more guesswork than science. Without solid data, it's nearly impossible to know if your team is operating at peak performance or if there's untapped potential waiting to be unleashed. This lack of insight doesn't just impact your cash flow; it can lead to overworked staff in some areas and underutilized talent in others.
By tracking movement patterns, time spent on tasks, and overall workflow, you gain invaluable insights into how your team really operates. With this knowledge, you can optimize processes, balance workloads, and identify areas where additional training or resources could make a big difference.
6. You Rely on Manual Data Collection and Reporting
In an era of smart technology, is your facility still stuck in the Stone Age of data management? Manual data collection and reporting are outdated, and they’re holding you back. Every minute your team spends logging numbers or updating spreadsheets is a minute lost from more valuable tasks. And let's face it—human error is inevitable. One small mistake in data entry can snowball into major planning mishaps or costly production errors. And with the average cost of a single lost hour ranging from $39,000 to more than $2 million, you can't afford to rely on outdated methods that put your operation at risk.
Spatial intelligence automates your data collection and reporting, creating a seamless flow of information across your entire operation. Sensors and AI do the heavy lifting, capturing and analyzing data in real time. This means no more end-of-day scrambles to compile reports or Monday morning surprises when you finally crunch last week's numbers. Instead, you have a constant pulse on your operations, allowing you to make informed decisions quickly and confidently.
7. You Struggle to Identify and Address Safety Hazards
Safety in manufacturing isn't just about following regulations - it's about creating a culture where every worker goes home unharmed every day. But if you're relying solely on incident reports and reactive measures, you're always one step behind. This approach not only puts your workers at risk but also exposes your business to potential legal and financial consequences.
Spatial intelligence transforms your approach to safety from reactive to proactive. By leveraging real-time data from sensors and AI-powered analysis, you can spot potential hazards before they become incidents. Imagine being able to identify high-risk areas, detect unsafe behavior patterns, or even predict equipment failures that could lead to accidents.
8. Your Competitors Are Already Using Spatial Intelligence
Standing still is the same as falling behind. While you're grappling with age-old challenges, your competitors are already reaping the benefits of spatial intelligence. They're optimizing their processes, enhancing worker safety, and boosting manufacturing efficiency in ways you might not even have imagined yet.
Implementing spatial intelligence isn't just a tech upgrade - it's a strategic move that can redefine your position in the market and give you a competitive edge. From streamlined operations to predictive maintenance, from enhanced safety measures to real-time decision-making capabilities, spatial intelligence can transform every aspect of your manufacturing process. Don't let your competition leave you in the dust.
Final Thoughts
The eight signs we've explored aren't just challenges; they're opportunities. Opportunities to transform your manufacturing floor from a reactive, inefficient operation into a proactive, intelligent powerhouse. Spatial intelligence isn't just about fixing problems; it's about fundamentally changing how you work.
AiFi provides the tools to make this transformation happen. Our spatial intelligence platform tracks people and objects through space to unlock valuable data and delivers real-time visibility, predictive analytics, and actionable insights, empowering you to optimize your entire operation.
Contact AiFi today to learn more and start your journey towards a smarter facility.